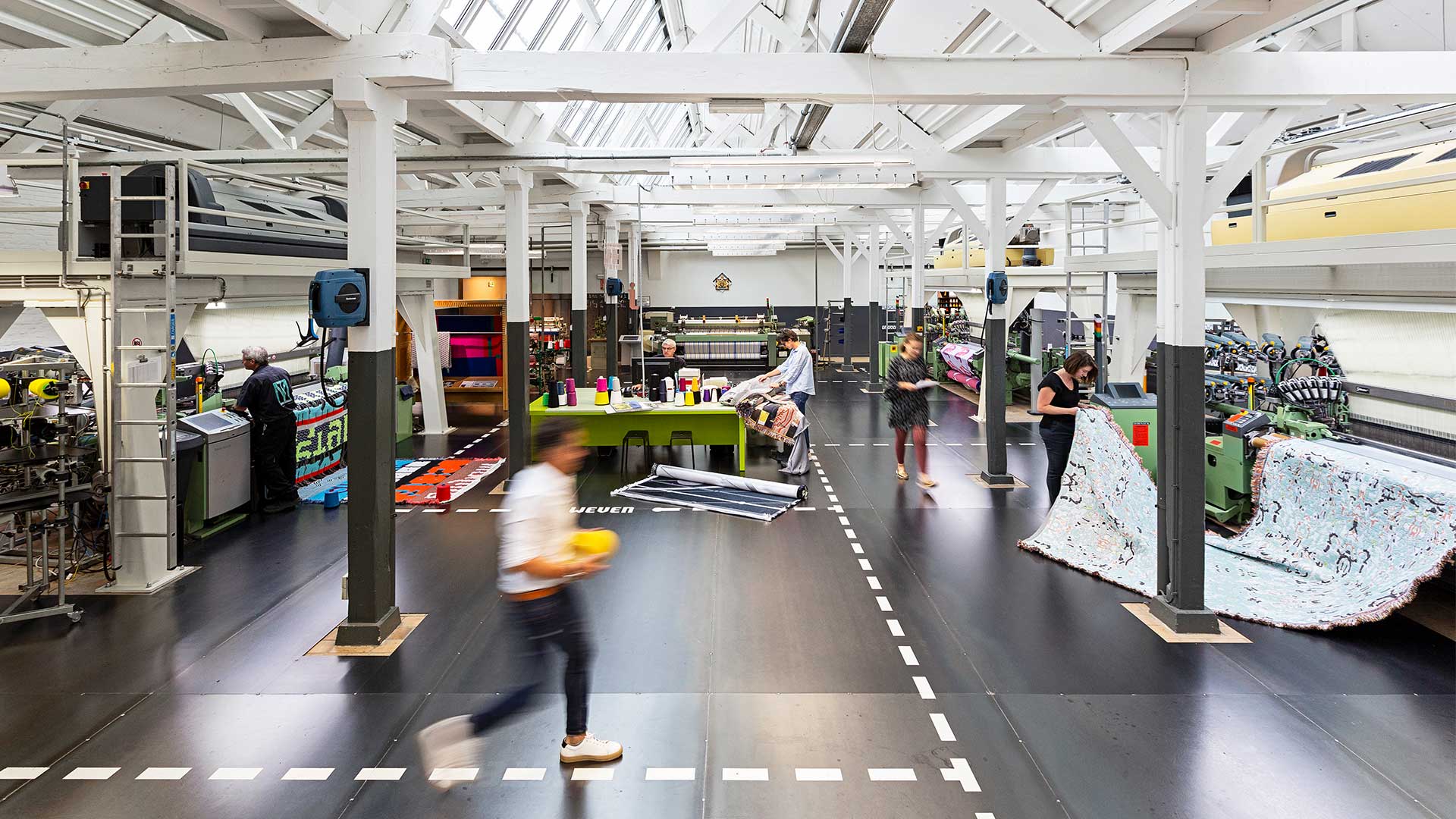
Make it in the TextielLab
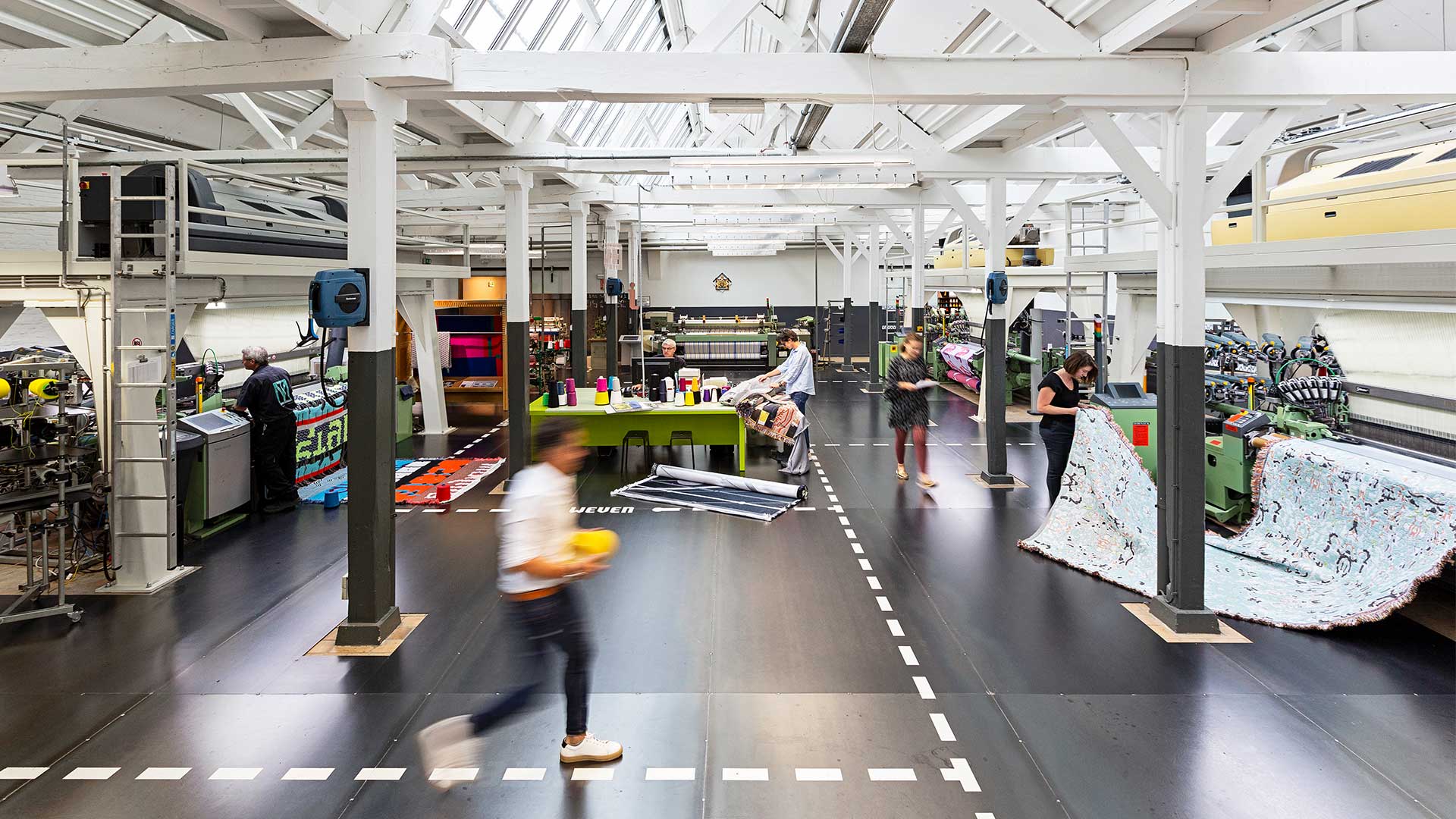
The TextielMuseum's professional workshop
Development space for makers
Welcome to the TextielLab, the beating heart of the TextielMuseum where craft, design and art meet. Interested in 3D weaving, knitted garments or embroidering with 15 needles at once? Supported by the knowledge and expertise of an experienced team, the TextielLab has everything you need to create and make your own textile (art)works.
News from the lab
Open Call: Metal Weaving
Mae Engelgeer upholsters the walls of TivoliVredenburg
Cadence: a new masterpiece by Otobong Nkanga
Meet the artists
1 / 4
Subscribe to our newsletter
And stay informed of the latest news